Electronic Overcurrent Relay Circuit Diagram
Every motor must be protected from all possible faults to ensure prolonged and safe operation as well as time loss caused due to breakdown. Almost all the industries rely on the electric motor to control its processes and production. Hence it is necessary to make the motor fail-safe.
Overload relay is one such device that protects a motor from damages caused due to overloads and over-currents. It is used with contactors and can be found in motor control centers and motor starters.
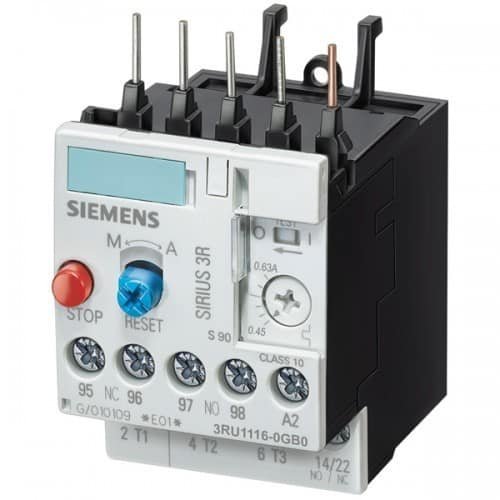
Definition of overload relay
An overload relay is a device that protects an electric motor against overloads and phase failure.
It senses overloading of motor and interrupts the power flow to the motor, thus protecting it from overheating and winding damages. Apart from overloads, it can also protect the motor from phase loss/ failures and phase imbalance. They are very commonly known as OLR.
What is an overload?
An overload is a condition at which a motor draws a current above its rated value, for a prolonged period.
It is the most encountered fault and can result in temperature rise in the motor winding. Hence the rapid return to normal operation is important.
Principle of operation
A thermal overload relay works in the principle of electro-thermal properties in a bimetallic strip. It is placed in the motor circuit in such a way that the current to the motor flows through its poles. The bimetallic strip gets heated up by the current directly or indirectly and when the current flow exceeds the set value, it bends.
They are always work in combination with contactors. When the bimetallic strips heat up, the trip contact is activated that in turn breaks the power supply to the contactor coil, de-energizing it and breaking the current flow to the motor. This tripping time is always inversely proportional to the current flow through the OLR. Hence higher the current flow faster shall it trips. Therefore, thermal overload relays are referred to as current dependent and inversely time-delayed relay.
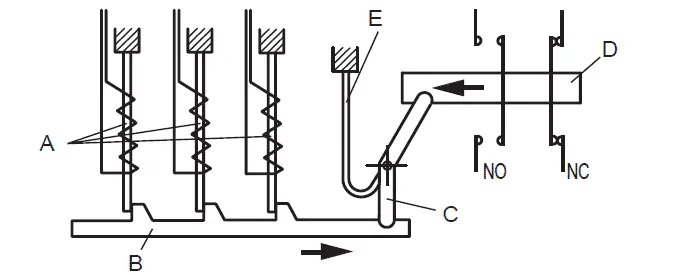
B = Trip slide
C = Trip lever
D = Contact lever
E = Compensation bimetal strip
Credit: Rockwell
Types of overload relays
Overload relays can be classified as follows:
- Bimetallic thermal overload relays
- Electronic overload relays
The working principle of the above differs a little from each other. Let us discuss it in the following sections.
As explained above, a bimetallic thermal relay works on heating property of bimetallic strip. In the direct heating method, the full current to the motor flows through the OLR. Therefore, it gets heated up directly by the current.
But in the case of indirect heating, the bimetallic strip is held in close contact with the current-carrying conductor inside the OLR. Excessive current flow to the motor heats up the conductor and hence the bimetallic strip. The conductor shall be insulated hence no current flow through the strip.

Working of electronic overload relay
Electronic overload relays do not have a bimetallic strip inside. Instead, it uses temperature sensors or current transformers to sense the amount of current flowing to the motor. It uses microprocessor-based technology for protection. Temperature is sensed using PTC and the same is used to trip the circuit in case of overload faults. Some electronic overload relays come with current transformers and Hall effect sensors that directly senses the amount of current flow.
The major advantage of electronic OLR over thermal OLR is that lack of bimetallic strip results in low heat losses inside the relay. Also, Electronic relays are more precise that the thermal relays. Some manufacturers build electronic relays with extensive features such as earth fault protection, motor stall protection etc. Electronic overload relays are much suited for applications that require a frequent start and stop of motors.
They are designed in such a way to withstand the starting current (which is typically 6 to 10 times the full load current) of the motor for a limited period (typically 15-30 seconds depending on the threshold of current).
Parts of a thermal overload relay
Apart from the bimetallic strip and contacts discussed in the working principle section, there are few more parts in an overload relay that needs to be mentioned.
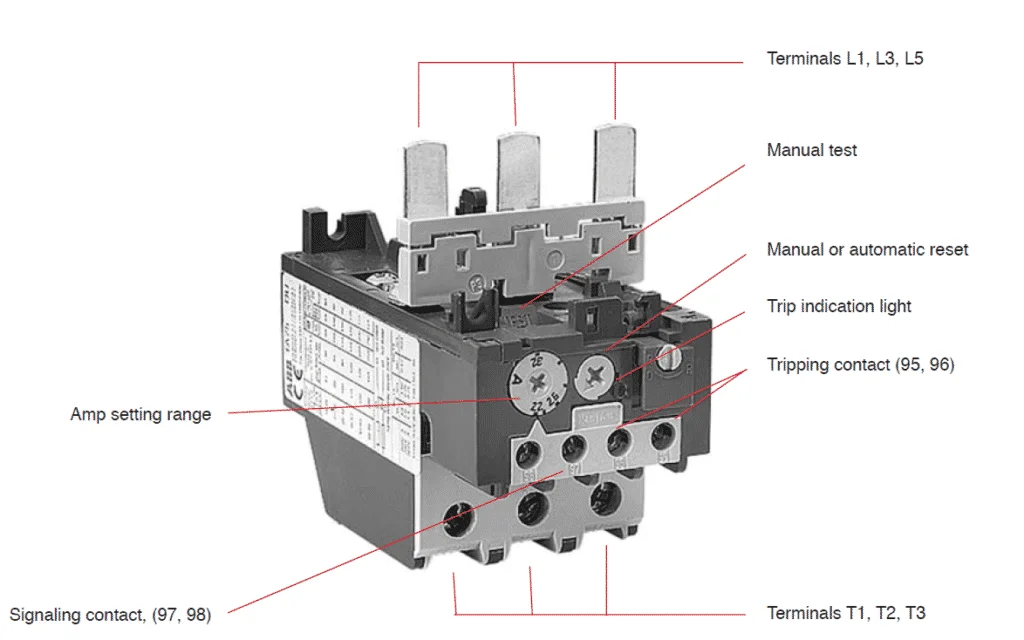
Terminal
Terminals L1, L2, L3 are input terminals. It can be directly mounted to the contactor. Supply to the motor can be connected to Terminals T1, T2, T3.
Ampere range setting
A rotary knob is present over the overload relay. Using this knob, the rated current of the motor can be set. The current can be set between the upper and lower limits provided. In the case of electronic overload relay, an additional knob for tripping class selection is also provided.
Reset Button
A reset button is present over the overload relay to reset the overload relay after a trip and clearance of fault.
Manual/Auto reset selection
With the manual/auto reset selection button, we can choose between manual and automatic reset of these relays after a trip. If the device is set to auto, a remote reset of OLR is possible.
Auxiliary contact
They are provided with two auxiliary contacts – one NO (97-98) and another NC (95-96). NO contact is for trip signaling and NC contact is for disconnecting the contactor. NC contacts should be capable of direct switching of contactor coil.
Test button
Using the test button, it is possible to test the control wiring.
Symbol of an overload relay
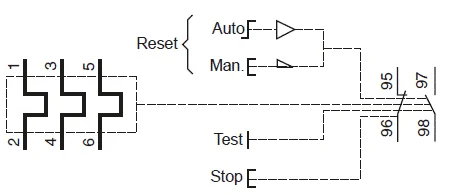
Here 1, 2, 3, 4, 5 and 6 are power terminal 95 & 96 are trip contacts and 97 & 98 are signalling contacts.
What is trip Class of overload relay?
The time taken by them to open the contactor during overloads is specified by the trip class. It is commonly classified into Class 10, Class 20, Class 30 and Class 5. The OLR trips in 10 seconds, 20 seconds, 30 seconds and 5 seconds respectively at 600% of full load current to the motor.
Class 10 and Class 20 are very commonly used ones. Class 30 overload relays are used for protection of motors driving high inertia loads and Class 5 relays are used for the motors requiring very fast tripping.
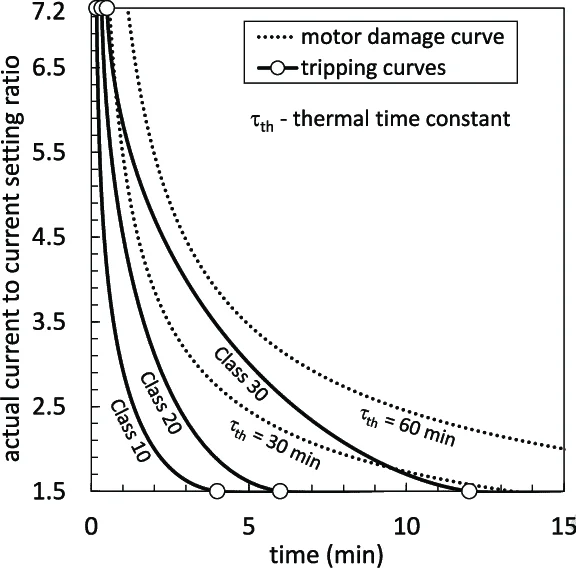
How to use an overload relay in a circuit?
They are always used in combination with the contactors in the circuit. It is connected in line with the motor such that the current to motor fully flow through it. Below are the various types of connections for single-phase and three-phase motors.
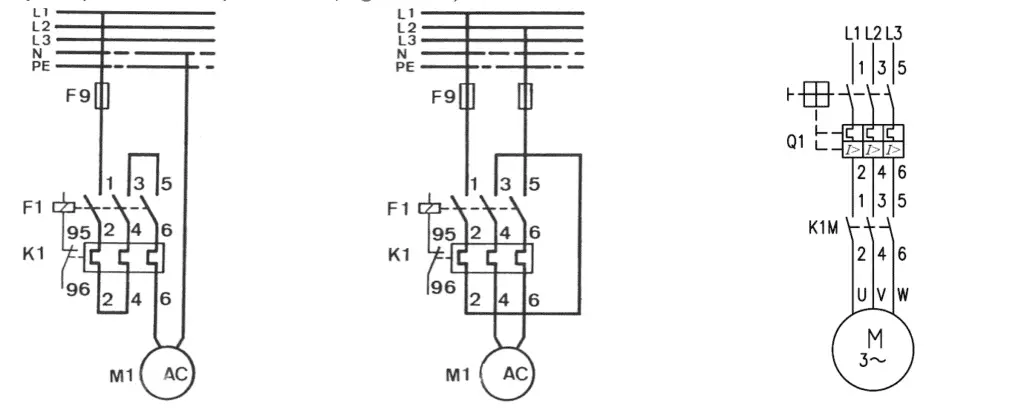
What causes the OLR trip?
As discussed above, there are three major conditions for overload trips:
- Overloading of the motor.
- Input phase loss
- Phase imbalance.
Apart from these, there may be some additional protection feature available. This varies from one manufacturer to the other.
How does an overload relay protect from phase failures?
During normal operation, the current flowing through each pole of an overload relay to the motor remains the same at a time. If anyone of the phase is interrupted, the current through the other two phases rises to 1.73 times the normal value. Hence the overload relay gets heated up and it trips. Phase failure is also known as single phasing of motor or phase loss.
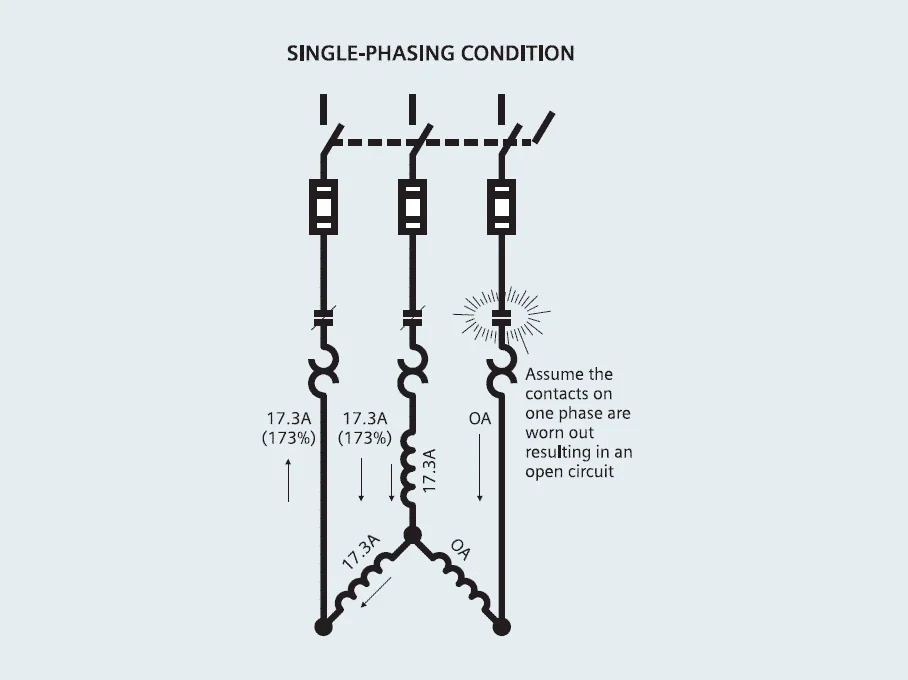
Can OLR protect from short circuits?
Overload relays cannot protect against short circuits. They should always be used with short circuit protection devices. Otherwise, any short circuits in the motor can potentially damage them. They can protect against overloads, phase loss, and phase imbalance, but not short circuits.
Summary
Overload relay is a device that can protect a motor from overloads, phase failure and phase imbalances. Based on the principle of operation they are classified into thermal and electronic overload relay. Thermal OLR is based on the principle of deformation of a bimetallic strip on heating and the electronic overload relay is a microprocessor-based device.
OLRs are used in combination with the contactors. It opens the contactor whenever it senses a fault. The time taken by them in opening the contactor during overloads is specified by its trip class. Overload relays cannot protect against short circuits.
Related articles
Source: https://www.electricalclassroom.com/overload-relay-principle-of-operation-types-connection/
Posted by: homerdonchatesz.blogspot.com
Posting Komentar untuk "Electronic Overcurrent Relay Circuit Diagram"